This write-up is to detail the cause of injector failures which have become common in our cars. This will also help in understanding the internal makeup and operation of an injector. First, the most common symptom of injector failure is a rough running engine. This is because one or more cylinders are not firing due to the lack of fuel in the cylinder. Second, the two most common ways of identifying a bad injector is by either (1) listening for an audible click to be heard in the injector or (2) using an ohm meter and measuring the resistance across the two injector terminals which should be close to a reading of 12 ohm. Operation of the injector. In 1990-1994 Zs the injectors have a constant voltage of +12 volts DC on one pin of the injectors at all times. This is whether the car is started and running or whether the car is not running and turned off with the ignition key removed. In 1995 a change was made which removed this constant voltage. The constant voltage going to the injectors in 1995 and earlier Zs is only present after the ignition switch is turned on. The voltage is then provided to the injectors through a relay. The injectors are activated (turned on) when a ground is supplied to the other of the two injector terminals. The ground is provided to the injectors by the cars ECU. OEM 370cc Twin Turbo Injector. Below is a picture of how an injector may look after you pull it out of the fuel rail. In this picture there is some plastic missing around the top of the injector due to damage caused by grabbing it with vise grips in order to pull the injector out. Over years of sitting in the fuel rails these can become pretty stubborn to get out and pulling them from the top of the engine without removing the plenum doesn't make it any easier.
 Parts that make up the injector. 
Internal operation of the injector. Thanks to member "lazer(NV)" for allowing me to use his picture. 
When the injector is deactivated the pintle moves in the opposite direction with the assistance of the return spring. This closes off fuel to the cylinder. The only thing in the injector that moves during its operation is the pintle and the return spring. The pintle assembly, and I call it an assembly because the pintle is actually made up of more than one part, is assembled to be held into the injector after in has been placed into the body of the injector. The pintle has a retainer that is attached to keep the pintle from coming out. The retainer is attached by a riveting process. In the picture below you are looking inside the top of the pintle as it sits in the lower body of the injector. You can see the retainer attached to the pintle by the rivet. One end of the return spring sits inside this part of the pintle. 
In the picture below, from the natural uncompressed size of the spring, there appears to be significant room for the pintle to travel. Of course this is not the actual distance between parts as they would be once in a closed injector. Actually, the pintle movement is only a fraction of a millimeter up and down. You have to look closely in order to see it move.

In the picture below you are looking at the top part of the injector body. There are two holes in this part of the injector to allow the electrical post of the solenoid to protrude. There are also two small O-rings that are used to surround the post to keep moisture out and to provide insulation between the post and the injector body.

When an injector fails or starts failing you will see either an increase in the amount of resistance during an ohm reading or no reading at all due to an open condition between the two injector terminals. In the injectors I have examined I have found no damage of the internal solenoid wires and no sign of breakdown of the material of the solenoid casing which would allow fluid to enter the area of the solenoid wires. In the picture below is an injector with the fuel filter screen removed. I angled the camera so you can see light through one of the holes on the other side of the injector. In the hole you can see the body of the solenoid and how it partially blocks the fuel entry at the hole. This blockage may seem a lot but compared to the hole that is opened by the pintle for spraying fuel it is quite large.

What keeps the solenoid from moving down into the injector body which would further block the fuel entry hole are three little feet that are spaced evenly apart from one another. These feet are part of the solenoid body. In the picture below of a cut away solenoid you can see two of these feet.
 At the bottom of the picture below is the spring guide. The spring guide is made of brass and is non-magnetic. The spring guide has grooves cut into it at one end. These grooves are used to help it hold to an epoxy which is used to hold the spring guide in place at the top of the injector. The O-ring in the center of the spring guide is used to hold the guide in a center position and to keep fuel from entering the top part of the injector.
 In this picture below you can see the top of the spring guide which is on the outside of the injector. When the properties of the epoxy that hold the spring guide have been compromised you can use a pair of pliers and grab the top of the spring guide and turn it by hand. If you tap on the top of the spring guide to further break loose the epoxy you can actually remove the spring guide from the injector by grabbing the top of the spring guide with pliers and pull it out while giving it a twisting motion. A lubricant also helps as the O-ring tends to grab the inside when it is dry.
 The main culprit that is causing the injectors to fail is the breakdown in the connection of the wires from the solenoid to where they connect to the electrical post. This breakdown is because of corrosion at these contacts. The cause of the corrosion is because there has been a breakdown in the epoxy which holds the spring guide due to ethanol in the fuel. It is also possible that the ethanol has increased the chance of leakage of fuel past both the O-ring of the spring guide and the O-rings which insulate the electrical post. In this picture below you can see the corrosion at the area of the post. You can also see the solenoid wire that is wrapped around the one post that is present on the right. The breakdown in these connections cause a high resistance or open condition between the two injector pins as seen when you take an ohm reading between the two injector terminals.
 It is thought that a process called electrolysis may be a contributing factor to the corrosion. For this to occur in this situation it is necessary to have both the negative and the positive terminals of the injector submerged in the fuel. If you take an ohm meter and take a reading between an injector in a fuel rail and to the fuel rail itself you will find that the injector is insulated from the fuel rail. This is because of the O-ring that is around the injector, the O-ring that is at the bottom of the injector and the plastic at the top of the injector which comes between the injector body and the metal plate on top of the injector which holds the injector to the fuel rail. The picture below shows how a path can can be made between the positive injector terminal and ground through the fuel. A condition which will cause electrolysis.
 If you want to see electrolysis in action, it can be observed by attaching wires to the leads of a nine volt battery and placing them in a glass of water. In a matter of seconds you will see bubbles begin to form around the exposed electrical wire in the water. Although it takes time, eventually the wires will begin to desolve due to the effects of electrolysis. Although electrolysis could and is most likely a contributing factor in the corrosion of the injector terminals it is not a necessary contributer due to the fact that just the fuel leakage alone is enough to degrade the area of the electrical contacts and speed the corrosion process. Unfortunately there is no way to remove the top of the injector in an effort to clean up the corrosion and re-solder the solenoid wires to the electrical post. And even if you could the integrity of the injector has still been compromised by the fuel leakage. The only thing to do is to replace all of the injectors with new style injectors or to replace the old style injector with a know good one. Of course in time the later mentioned fix will only result in what you see above. I hope this has helped to shed some light on what is going on with our failing injectors. Good luck with yours!
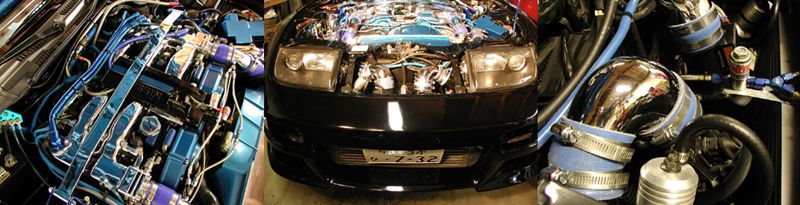 (Total Mouse Over Hits: a Lot) www.mytwinturbo.com Watch an ECZA meet caravan! Download my Nissan 300ZX Vin/Model Lookup |